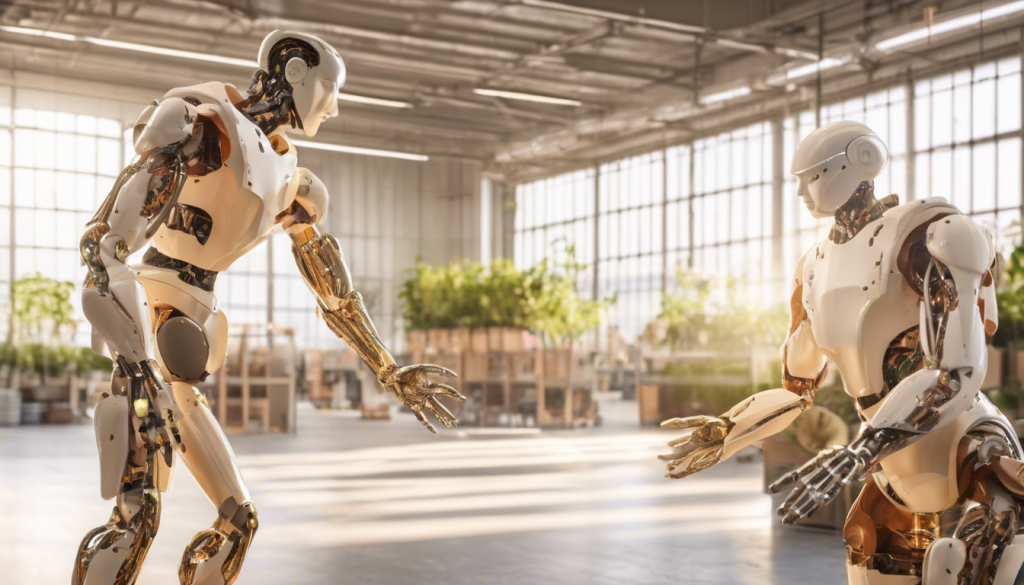
The Rise of Humanoid Robots in the Workplace: Balancing Opportunity and Challenge
The first humanoid robot in a Chinese automotive plant has just completed its 17-hour shift assembling vehicles, working alongside human colleagues who are still adjusting to their mechanical counterpart. This isn’t science fiction—it’s happening right now in manufacturing facilities around the world, and it represents just the beginning of a workplace transformation that will reshape how we think about labor, productivity, and human-machine collaboration.
The Growing Market for Workplace Humanoids
The humanoid robot market is experiencing rapid growth that shows no signs of slowing. Currently valued at approximately $1.5 billion in 2023, the market is projected to grow at a staggering compound annual growth rate (CAGR) of 63.5% from 2024 to 2030, according to research cited by IDTechEx.
For perspective on the long-term outlook, Morgan Stanley Research forecasts that by 2050, the humanoid robot market could reach $5 trillion, with more than one billion units deployed globally. China is expected to lead in deployment numbers by mid-century, followed by the United States, as reported in Morgan Stanley’s analysis.
Where Humanoid Robots Are Making Their Mark
Manufacturing and Automotive Industries
The automotive industry stands as an early adopter of humanoid robots. Chinese automotive manufacturers have achieved nearly 100% automation in their body shops using these robots. For example, NIO operates 300 robots with just a dozen workers, producing 20 vehicles per hour, according to a Harvard Business Review analysis.
BMW has reported a 400% efficiency boost after deploying humanoid robots at its Spartanburg plant. Meanwhile, Schaeffler plans to deploy Agility Robotics’s Digit humanoid robots across its 100 plants globally by 2030 to automate physically demanding tasks.
Elder Care and Disaster Response
Beyond manufacturing, humanoid robots are prime candidates for use in elder care, where their human-like dexterity and interaction capabilities could provide valuable support. They’re also being developed for disaster response scenarios, where they can perform in environments too hazardous for human workers.
What This Means For You
If you work in manufacturing, logistics, or any industry with repetitive physical tasks, humanoid robots will likely enter your workplace within the next decade. Rather than fearing replacement, consider how your role might evolve to work alongside these machines. The most successful professionals will be those who can collaborate effectively with robotic systems, focusing on tasks requiring human creativity, problem-solving, and interpersonal skills.
Technical Capabilities and Limitations
Current Capabilities
Humanoid robots are designed to perform tasks in environments built for humans, making them suitable for a wide range of jobs without significant reconfiguration. Their human-like bodies allow them to collaborate with humans more effectively than specialized robots.
Recent advances in AI and simulation technology have made training humanoid robots more efficient. For example, Nvidia’s GR00T Blueprint and Figure AI’s VLA model Helix can master multiple tasks in a short time, improving their cost-effectiveness, as highlighted in recent technical analyses.
Current Limitations
Despite impressive advances, humanoid robots are just beginning to transition from research labs to commercial use. Boston Dynamics’ Atlas, for instance, is expected to be deployed in a Hyundai factory later this year, but such commercial deployments remain limited.
Training humanoid robots to master new skills can be time-consuming, even with advanced AI models. It typically takes about 500 hours of data for robots to master one new skill—a significant investment of time and resources.
Pro Tip:
When evaluating humanoid robot solutions for your business, focus less on the flashy demonstrations and more on proven use cases with documented ROI. Ask vendors for case studies within your specific industry.
Impact on Employment and the Workforce
The impact of humanoid robots on employment is still in early stages, with most effects being more about future potential than present job displacement.
While automation in manufacturing has already resulted in significant job losses, with 1.7 million manufacturing jobs lost in the US since 2000 according to Exploding Topics, the specific impact of humanoid robots is still emerging.
By 2050, about 90% of humanoid robots will be used for industrial and commercial purposes, which could result in significant job displacement in sectors with repetitive tasks. However, the development and maintenance of these robots will also create jobs in related sectors.
What This Means For You
If your job involves repetitive physical tasks, start developing complementary skills that robots can’t easily replicate. Focus on creativity, complex problem-solving, emotional intelligence, and strategic thinking. These human-centric skills will remain valuable even as automation increases.
Essential Skills for Human-Robot Collaboration
As humanoid robots become more common in workplaces, human workers need to develop specific skills to work effectively alongside them:
- Adaptability and Flexibility: Be open to learning new tasks and methods as robots are introduced into work environments.
- Robotics and AI Literacy: Develop a basic understanding of how robots operate, including their control systems and AI components.
- Communication and Collaboration Skills: Learn to clearly communicate with robots, either directly or via control systems, to ensure tasks are coordinated effectively.
- Problem-Solving and Troubleshooting: Develop the ability to troubleshoot and problem-solve when robots are not performing as expected.
- Training and Learning from Robots: Be willing to learn from robots, especially in tasks where robots can perform with high accuracy or efficiency.
Getting Started with Humanoid Robots
For businesses considering implementing humanoid robots, here are some practical first steps:
- Identify Appropriate Use Cases: Focus on repetitive, structured tasks that are physically demanding or potentially hazardous for human workers.
- Calculate ROI: According to a 2024 McKinsey & Company analysis cited by iFactory, manufacturers using advanced robotics have seen their ROI periods decrease from 5.3 years in 2019 to 2.8 years in 2023.
- Start Small: Begin with pilot projects in controlled environments before scaling up.
- Invest in Training: Prepare your workforce for collaboration with robots through comprehensive training programs.
- Consider Costs Beyond Purchase: Factor in integration, maintenance, and potential regulatory compliance costs.
Free and Low-Cost Alternatives
While full-scale humanoid robots require significant investment, smaller businesses can explore more affordable options:
- Collaborative Robots (Cobots): These smaller, more specialized robots can work alongside humans safely and cost significantly less than humanoid robots.
- Robot-as-a-Service (RaaS): Some providers offer subscription-based models, reducing upfront costs.
- Refurbished Industrial Robots: Previously used robots can be acquired at a fraction of the cost of new models.
- Open-Source Robotics Platforms: Communities like ROS (Robot Operating System) provide free software frameworks for robotics development.
Ethical Considerations
The integration of humanoid robots into the workplace raises several ethical considerations:
Workforce Displacement and Job Redesign
While robots can perform dangerous or repetitive tasks, this could affect job security for human workers. Companies should focus on job roles that involve creativity, problem-solving, and decision-making, which are tasks that robots cannot perform as effectively.
Worker Safety and Dependence on Robots
Robots must be integrated in a way that ensures worker safety. This includes rigorous safety validation and transparent communication about robot capabilities and potential risks, as emphasized by companies like Figure in their safety frameworks.
Bias and Fairness
The use of AI in robots requires careful scrutiny to ensure that automation processes do not perpetuate existing societal biases. Companies must ensure fairness in employment, wages, and quality standards.
In Other Words
Humanoid robots are mechanical workers designed to look and move like humans, allowing them to work in spaces built for people without requiring special modifications. They’re becoming increasingly common in factories, warehouses, and potentially care settings, where they can handle repetitive or dangerous tasks.
Recent Advancements to Watch
- AI and Machine Learning: Modern humanoid robots are equipped with AI that enables them to